1.熱成形概要
熱成形(真空成形・圧空成形)は、射出成形に比べ、以下のメリットがある。
① 成形品形状の片側の表面形状のみの金型で成形可能
② 空圧を利用して成形を行うため、金型に要求される強度が小さい
熱成形では、シート状の樹脂に対して、成形品の内側・外側どちらの面で成形を行うかによって、凹型と凸型の2種類が考えられる。
本事例では、図1に示す容器を成形する際、上記の凹型、凸型による違いをシミュレーション結果を用いて紹介する。
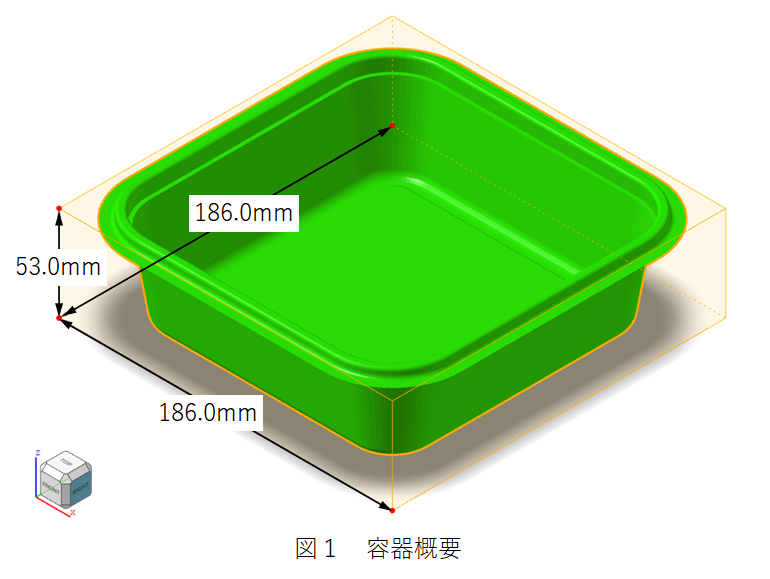
2.凹型と凸型
各型仕様による成形時のシート変形挙動を図2・3に示す。
凹型:成型品形状の内側を金型形状として、基本的に空圧を用いてシートを変形させ成形を行う。
凸型:成型品形状の外側を金型形状として、基本的に型移動を用いてシートを変形させ成形を行う。
図2 凹型を用いた成形時のシート変形挙動
図3 凸型を用いた成形時のシート変形挙動
3.金型仕様による板厚分布の差異
凹型、凸型で成形を行った時のシート板厚変化の解析結果を下図に示す。
図4 凹型成形時のシート板厚変化
図5 凸型成形時のシート板厚変化
下図に示す成形品断面(A-B)で板厚分布及び、板厚変化比*を金型仕様で比較した結果を図6・7に示す。
板厚分布は、最大・最小板厚差は凹型の方が小さく、底面部のみで比較すると凸型の方が小さい。
板厚変化比は、凹型では底面/外周部の形状段差部で、凸型では形状が変化する底面と縦壁の境界部で顕著に大きくなる。
*板厚変化比は、下図の様に距離に対する板厚差を表します。
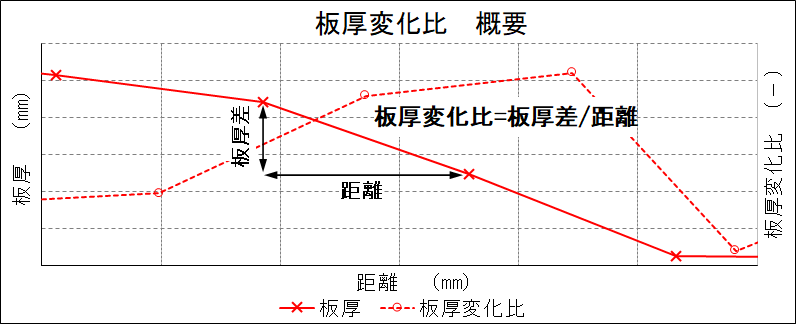
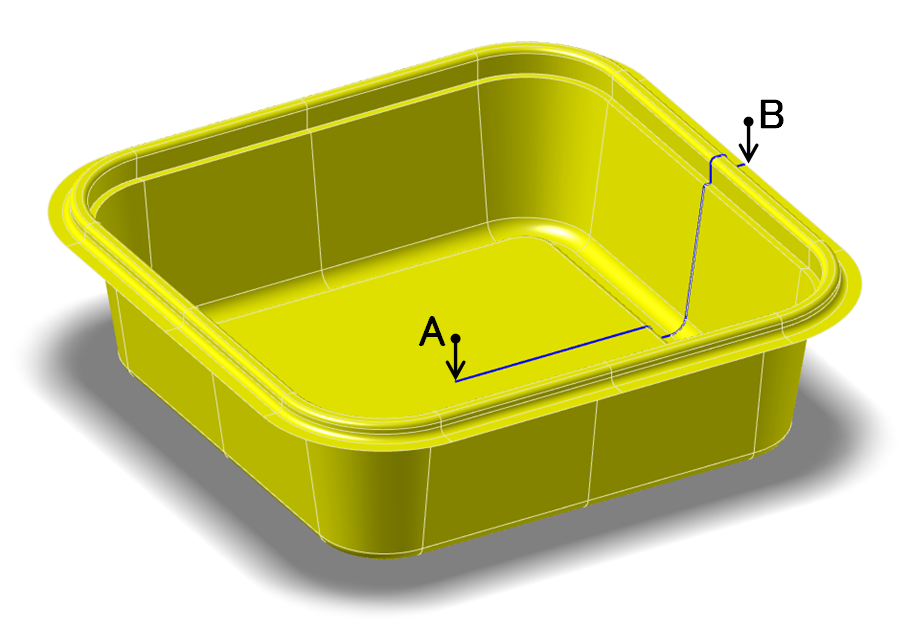

図6 型仕様による板厚分布比較
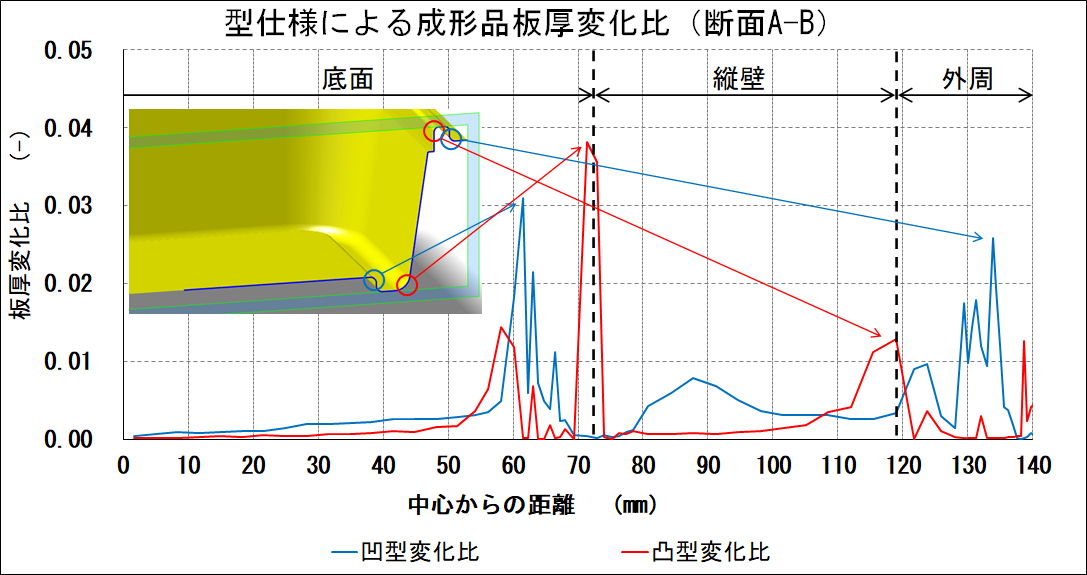
図7 型仕様による板厚変化比比較
4.まとめ
真空成形は、成形工法は簡易であるが、金型仕様によって板厚分布や板厚変化に特徴が表れる。
この事から、成形品に要求される品質、例えば「平面部での板厚差を限りなく小さくしたい」や「形状変化する部分での板厚差を小さくしたい」に対して、BlowViewを利用する事により、製品設計段階で適切な金型仕様を決定する事が可能となる。