熱硬化性樹脂の硬化反応を考慮した攪拌解析
1. はじめに
樹脂製品の成形プロセスでは、複数の材料を均一に混合する攪拌プロセスが成形不良や品質の面からも重要となります。
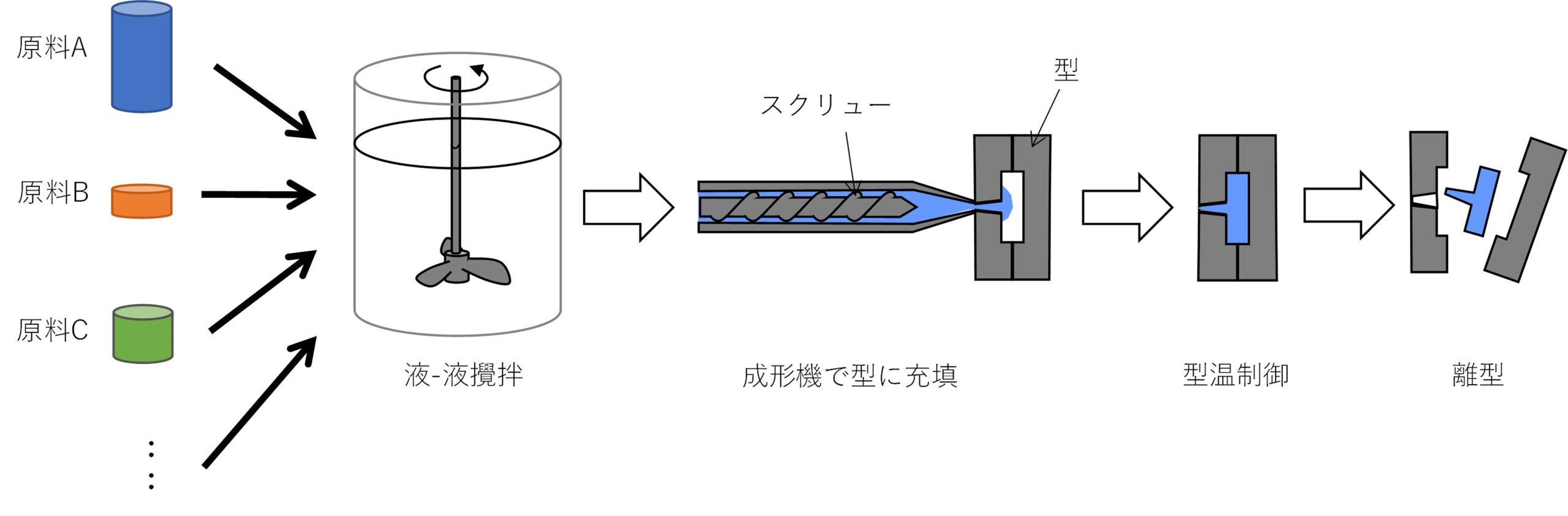
材料が不均一な状態で次の成形プロセスに進んでしまうと成形不良の原因となってしまうため、一般的に、攪拌時間延長や回転速度を上げる等の対策が取られます。一方、熱硬化性樹脂を考えた場合、反応遅延材や攪拌槽の温度等で調節するとはいえ、長時間の攪拌は硬化反応を進めてしまう要因になります。また、回転速度を上げるとせん断速度の上昇につながるため、硬化反応を進めてしまう危険性がでてきます。
流体解析ソフトを活用すると、実験に比べ少ないコストで適切な攪拌条件を調査する事ができますが、熱硬化性樹脂材料(主剤と硬化剤)の場合、攪拌中の各材料の広がりや硬化反応を考慮した計算が必要となるため、一般的な流体解析ソフトでは計算できません。そこでOpenFOAMのVOF法のソルバーであるinterFoamをカスタマイズして、攪拌中の主剤と硬化剤の濃度変化及び硬化反応を考慮したソルバーを開発しました。
2. カスタマイズ内容の説明
計算初期に配置した主剤と硬化剤は流れに乗って時々刻々変化し槽内に広がっていきます。また、硬化反応が起きるためには、同じセル内に反応に必要な量だけ、主剤と硬化剤が存在している必要があります。
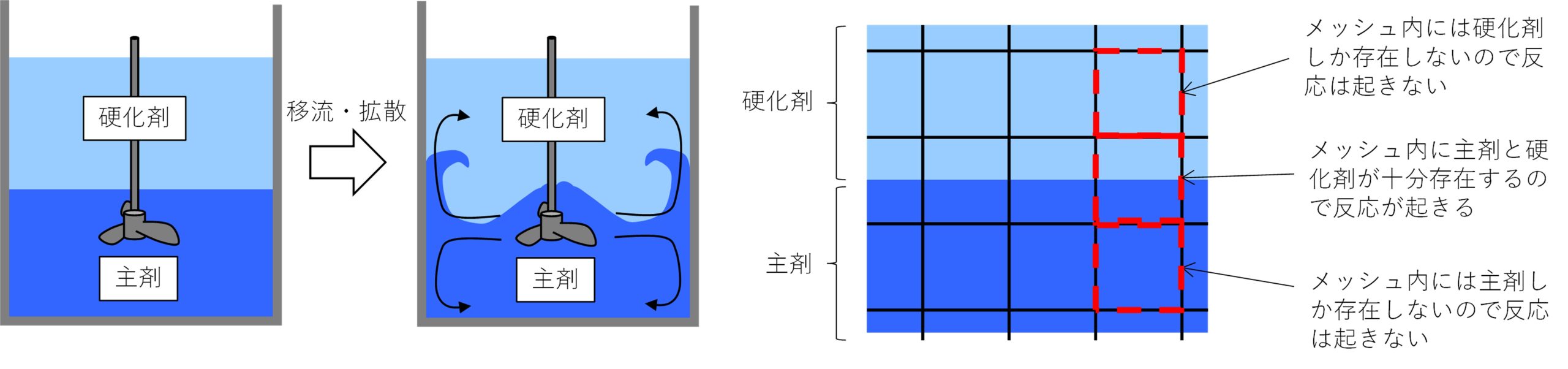
さらに、攪拌槽内では場所ごとに温度やせん断速度が異なるため反応の進み具合が異なります。このため、硬化反応の進行状況、主剤、硬化剤を物質種の移流拡散方程式(Species equation)で計算します。
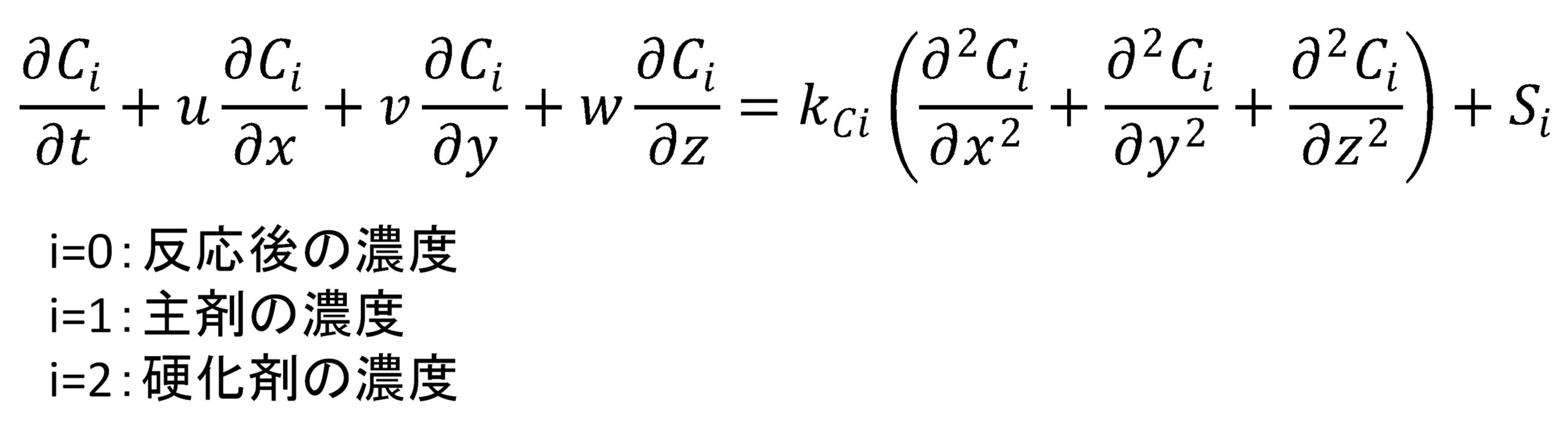
この際、硬化反応の上昇分に応じて、セル内の主剤と硬化剤の濃度を減少させます。
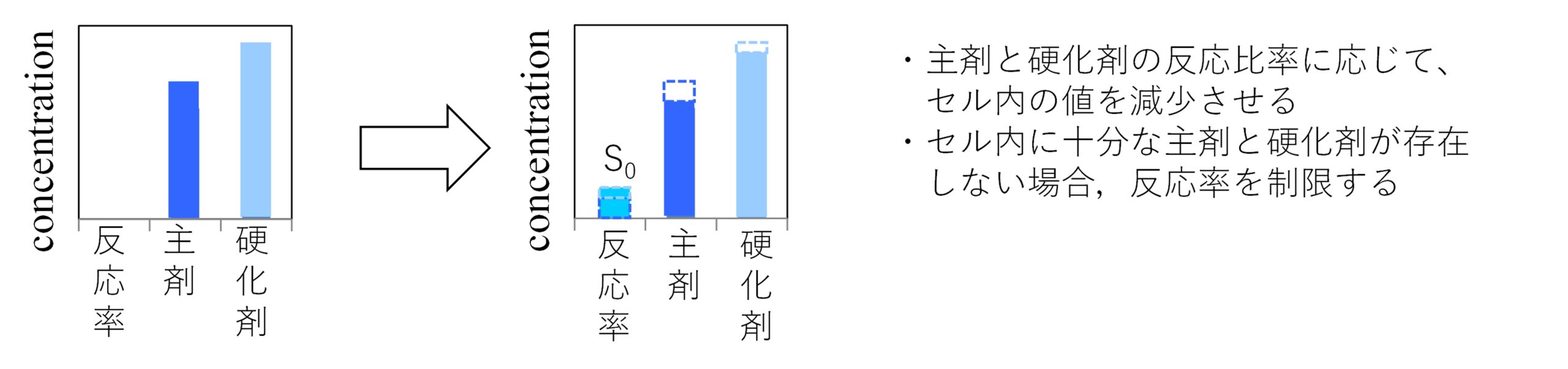
また、interFomaソルバーは熱計算に対応していないためエネルギー方程式も追加します。

3. 硬化反応と粘度モデル
新たに粘度モデルを追加し、硬化反応の反応速度をKamalモデルで、粘度モデルをMacoskoモデルで計算します。
(補足:式中の未知パラメータは材料固有の値です。DSCやキャピロリーレオメータ―等の実験データからパラメータフィッティングして算出する必要があります。なお、弊社は、実験データからパラメータフィッティングするサービスも承っております。)
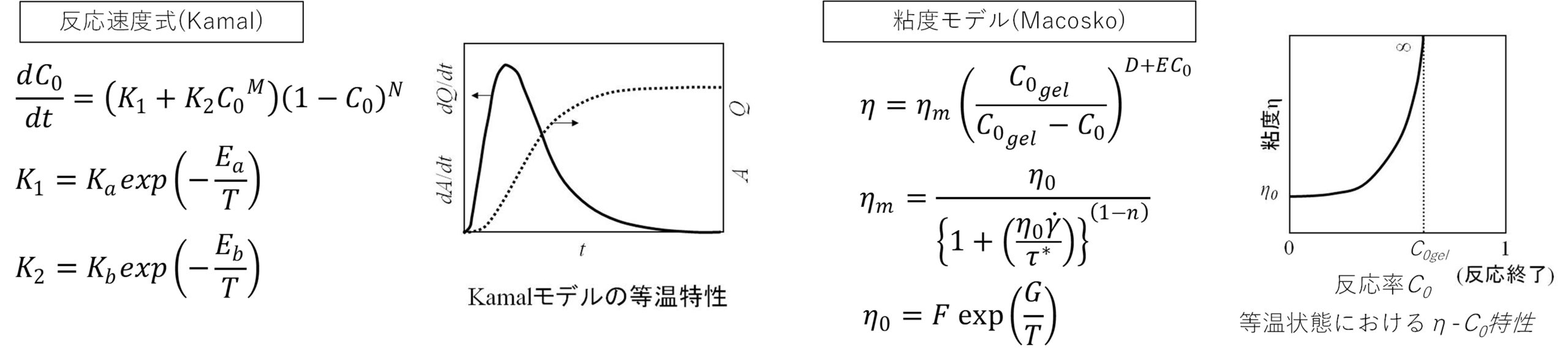
4. 解析事例
4-1 モデル概要
攪拌中の硬化反応が考慮可能なソルバーの機能紹介として、図1に示す攪拌槽の混合解析を実施し,槽内の主剤と硬化剤の濃度変化と硬化反応の進行状態を調査します。計算は3次元-非定常-非圧縮解析とし,40秒間の計算とします。また,初期温度は60℃とし、主剤と硬化剤の反応比率は1:1とします。

4-2 計算条件
図2に境界条件を示します。
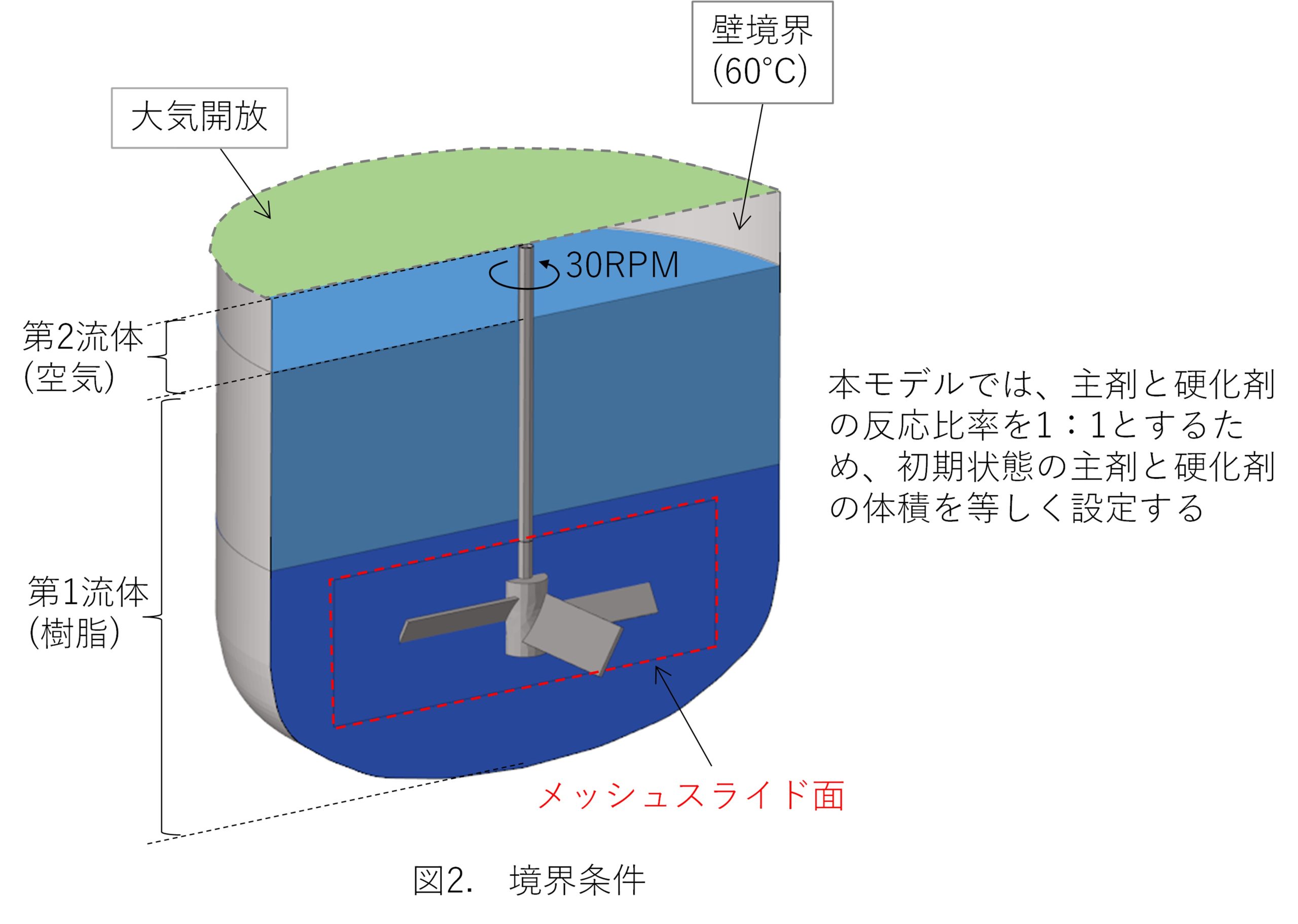
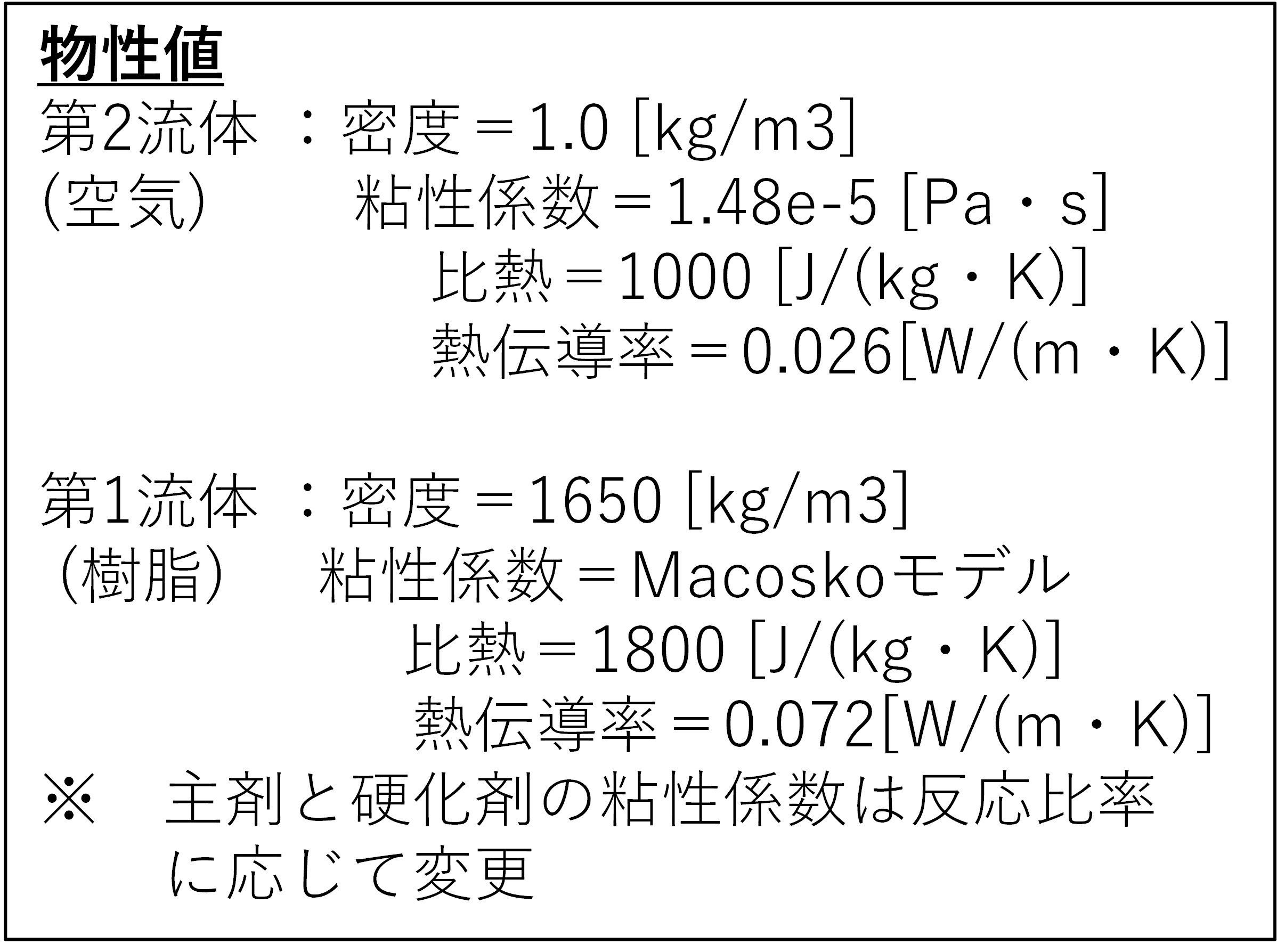
本来であれば、KamalモデルとMacoskoモデルのパラメータは、材料固有の値のためDSCやキャピラリーレオメータ等の実験データから算出する必要がありますが、今回はソルバー機能の紹介が目的のため、仮の値を定義して計算します。図3と図4に、本解析事例で設定したパラメータの粘度特性と反応率特性を示します。
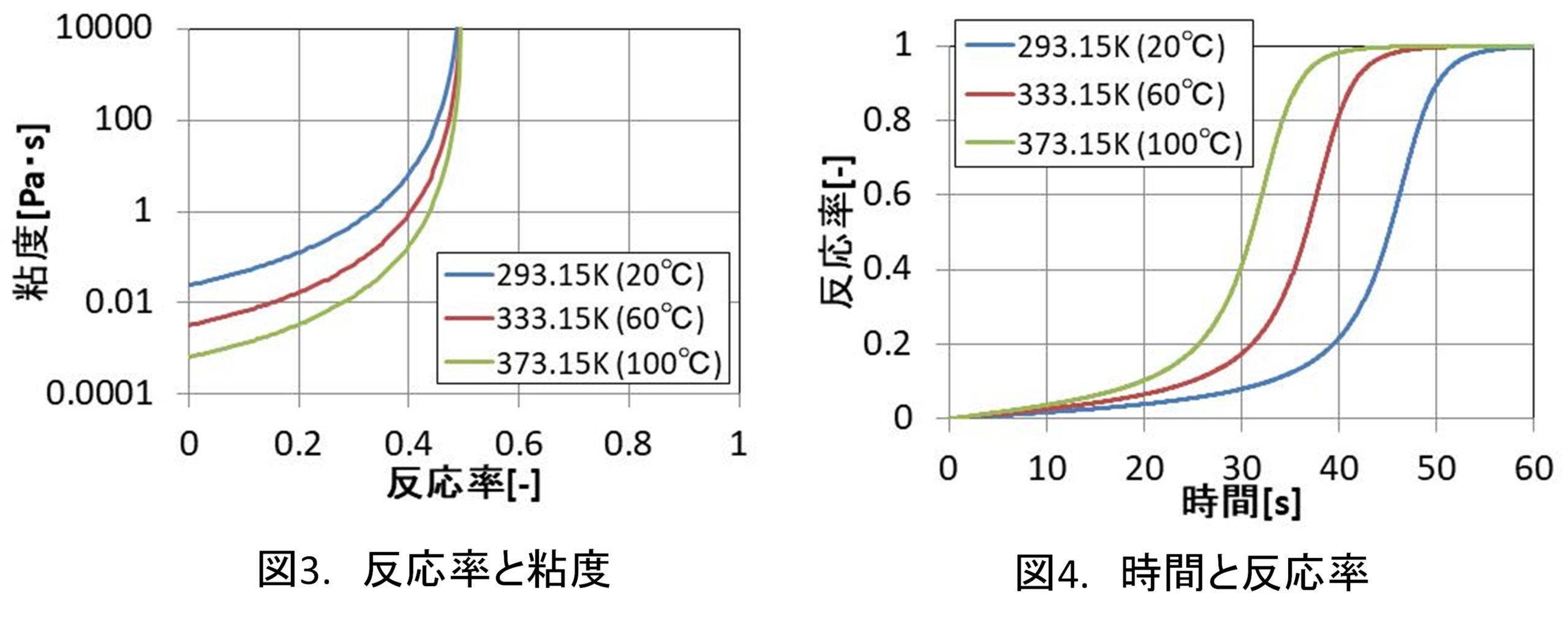
4-3 計算結果
図5に流線のアニメーションを示します。
図5 流線のアニメーション
図6に代表時刻における垂直断面の流速を示します。
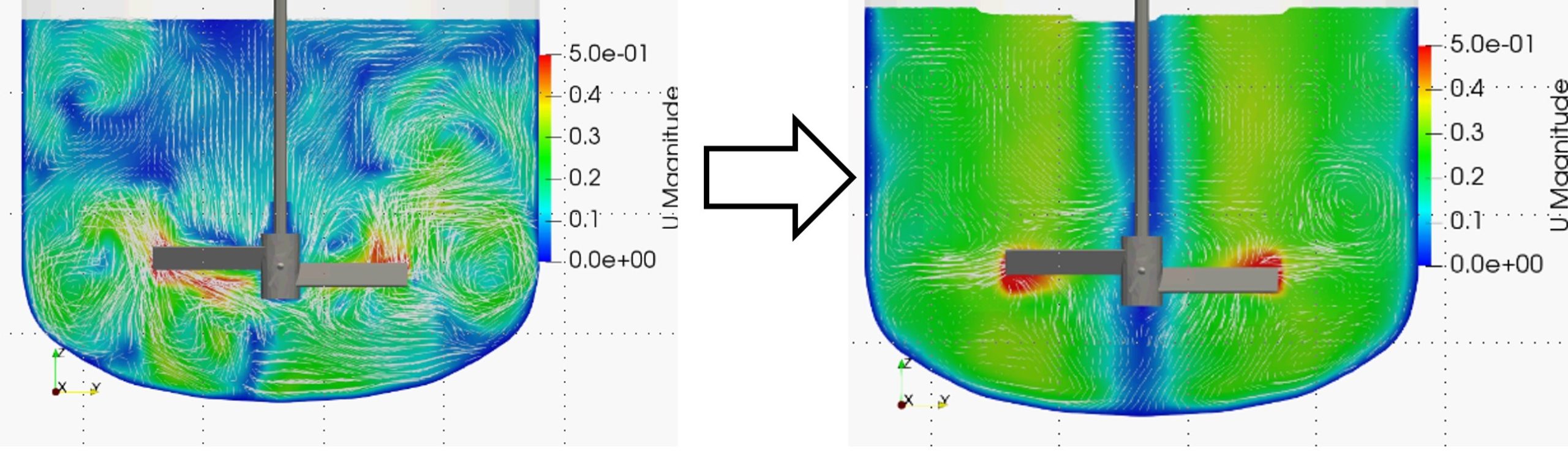
図6. 代表時刻における垂直断面の流速[m/s]
図7に代表時刻における中心断面の温度を,図8に中心断面の反応率を示します。
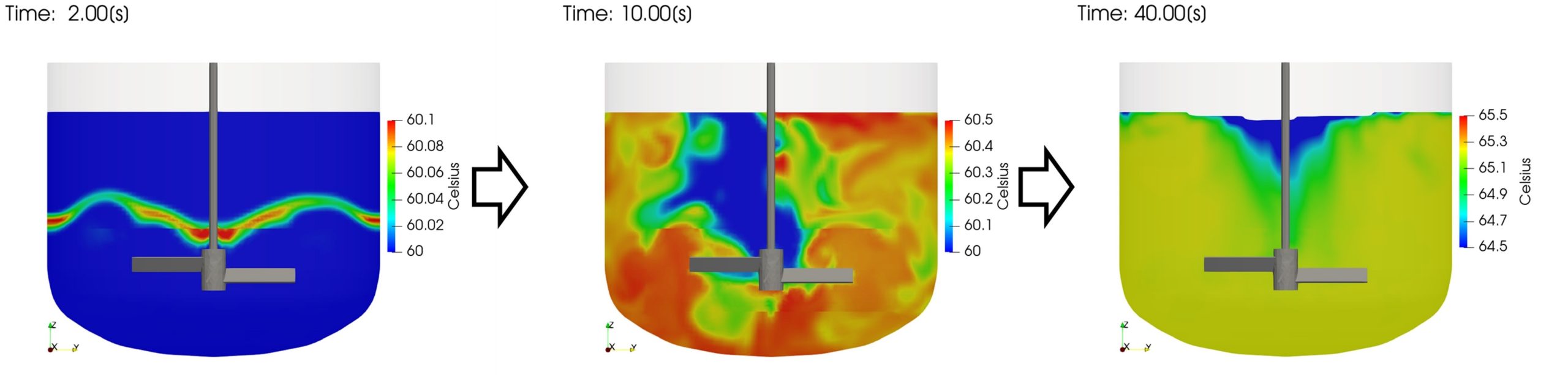
図7. 中心断面の温度[℃]
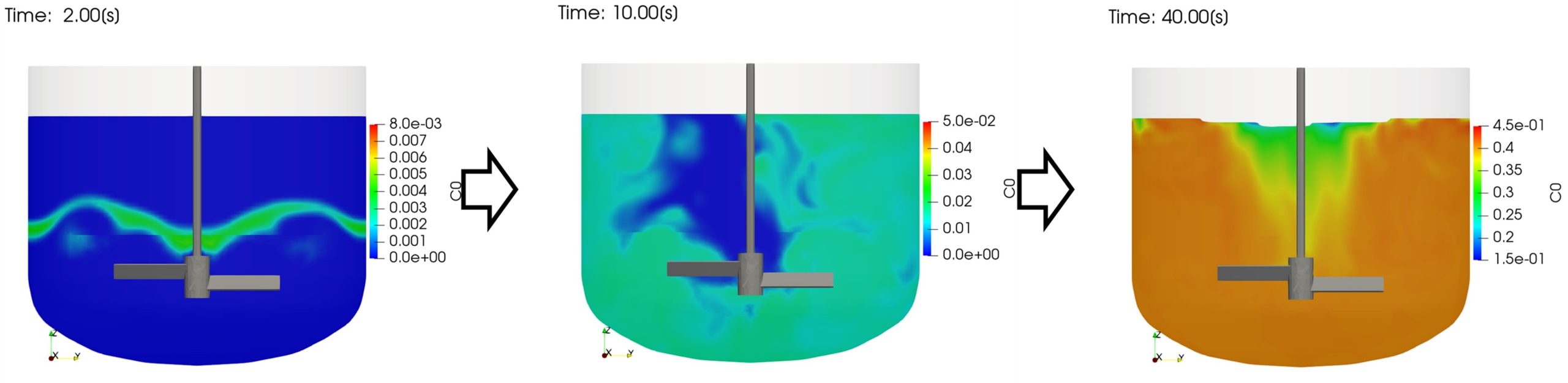
図8. 中心断面の反応率[-]
図9に、主剤濃度の等値面(Iso-surface)のアニメーションを示します。
図9 主剤濃度の等値面
反応が進むにつれて、槽内の主剤濃度は減少していきます。ただし、40秒の時点でも槽内の主剤濃度が均一になっていないことが確認できます。特に軸周辺で不均一な状態が残りやすい傾向がみられます。このような場合、攪拌時間を延長しても均一な状態にはなりにくいため、邪魔板(バッフル)の配置等の対策が必要になります。
5. まとめ
interFoamソルバーをカスタマイズし、原料が分離した状態で攪拌槽内の硬化反応が考慮可能なソルバーを開発しました。
・ 攪拌槽内の反応率の分布や進行状況を確認できます
・ 反応せずに主剤が残りやすい場所等を確認する事ができます
・ 翼形状や回転速度.邪魔板の有無等,理想的な攪拌条件の検討に使用できます